Dans un monde économique où l’excellence opérationnelle est devenue un impératif, la quête de l’amélioration continue s’impose comme une priorité stratégique pour toutes les entreprises. De Toyota à Michelin, en passant par General Electric, les grands groupes ont compris depuis des décennies que le succès durable repose sur un processus d’adaptation permanent, basé sur la rigueur et l’innovation managériale. La roue de Deming, souvent désignée sous l’acronyme PDCA (Plan-Do-Check-Act), se démarque comme un outil incontournable dans cette dynamique. Il ne s’agit pas simplement d’une méthode parmi d’autres, mais d’un véritable catalyseur d’efficacité et de qualité, capable de transformer les organisations en environnements apprenants capables de se réinventer continuellement. Que ce soit dans l’industrie automobile avec Honda et Ford, dans la logistique avec DHL, ou dans l’agroalimentaire avec Nestlé, la roue de Deming structure le pilotage des améliorations et l’optimisation des performances opérationnelles. Cette analyse détaillée dévoilera les fondements, la méthode et les applications concrètes de cette approche, offrant ainsi aux décideurs un levier puissant pour piloter la transformation de leurs entreprises.
Origines et fondements historiques de la roue de Deming : une méthode née du besoin d’excellence
Le cadre conceptuel de la roue de Deming trouve ses racines dans les travaux du statisticien américain William Edwards Deming, dont l’influence dépasse largement les frontières de son pays d’origine. L’après-Seconde Guerre mondiale marque un tournant décisif pour l’industrie mondiale, car les méthodes traditionnelles de gestion de la qualité montrent leurs limites face aux exigences croissantes. Deming intervient alors au Japon, où il devient l’architecte principal d’une révolution industrielle fondée sur l’innovation continue des processus. Grâce à son approche itérative PDCA, le Japon opère une transformation spectaculaire qui propulse les entreprises nippones à l’avant-garde mondiale. Toyota, Mazda et Honda incarnent aujourd’hui l’héritage de cette méthode, mettant en œuvre des itérations constantes visant la perfection dans leurs chaînes de production.
La méthode PDCA, déconstruite en quatre étapes cycliques – Planifier, Faire, Vérifier, Agir -, repose sur un principe simple mais puissant : l’amélioration s’obtient par l’expérimentation contrôlée et l’analyse systématique. Ce cycle assure une progression maîtrisée et évite les risques liés à des changements impulsifs ou non validés. En cela, la roue de Deming s’inscrit parfaitement dans la philosophie du Lean Management, une autre création d’origine japonaise destinée à éliminer les gaspillages et maximiser la valeur pour le client.
- Plan : Élaborer un plan fondé sur une analyse précise des besoins et des processus.
- Do : Exécuter ce plan à une échelle réduite pour minimiser les risques.
- Check : Contrôler et évaluer les résultats obtenus par rapport aux objectifs.
- Act : Standardiser les améliorations ou ajuster la démarche selon les retours.
Année | Événement clé | Impact |
---|---|---|
1920s | Walter A. Shewhart développe le cycle Plan-Do-See | Fondation des méthodes d’amélioration continue |
1950 | William Edwards Deming introduit le PDCA au Japon | Démarrage du « miracle économique japonais » |
Années 1980 | Diffusion du PDCA en Occident, notamment chez General Electric | Révolution des pratiques de qualité et de management |
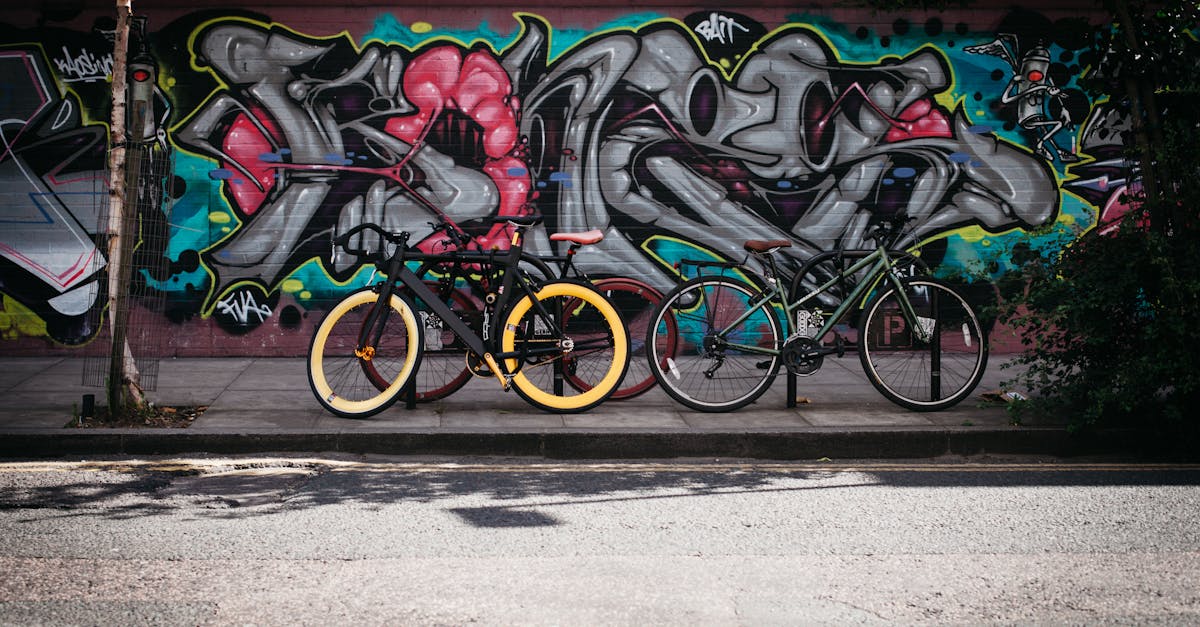
Les quatre étapes clés de la roue de Deming : décryptage et application opérationnelle
La force de la méthode PDCA réside dans la simplicité et la systématicité de ses quatre phases, qui se combinent pour créer un moteur puissant d’amélioration continue. Exploiter concrètement chaque étape est essentiel pour une mise en œuvre réussie, notamment dans des secteurs concurrentiels comme l’aéronautique avec Boeing ou l’électronique avec Sony.
Plan : L’étape stratégique de réflexion et de préparation
Au cœur de la prévention des erreurs et de l’optimisation des ressources, cette phase requiert une analyse rigoureuse de la situation initiale. On recense les dysfonctionnements, les opportunités et les besoins à travers des outils tels que l’analyse SWOT, indispensable pour identifier les forces, faiblesses, menaces et opportunités. À Nestlé, cette approche organisée permet de définir clairement des objectifs chiffrés et alignés avec la stratégie globale.
Quelques pratiques essentielles à cette phase :
- Définition précise des objectifs et des résultats attendus.
- Collecte exhaustive des données pertinentes.
- Allocation claire des ressources humaines et matérielles.
- Élaboration d’un planning détaillé avec jalons critiques.
Do : Tester et expérimenter à petite échelle
La mise en œuvre initiale s’effectue lors d’un essai réduit, dans le but de limiter les risques et de maîtriser les variables. Dans ce contexte, le pilotage est crucial, notamment chez Ford où chaque modification est d’abord mise en œuvre sur des lignes pilotes avant une généralisation. La documentation systématique des actions facilite la traçabilité et l’identification des causes en cas de déviation.
- Réalisation de projets pilotes.
- Enregistrement méticuleux des processus et interventions.
- Surveillance constante des premières tendances.
Check : Mesure et évaluation rigoureuses des résultats
Vient ensuite l’interprétation des données collectées, afin de mesurer l’écart entre objectifs et résultats effectifs. Michelin utilise des indicateurs de performance clés (KPI) pour quantifier les avancées, permettant de s’appuyer sur des éléments tangibles pour valider l’efficacité des changements. Par ailleurs, le feedback des équipes sur le terrain contribue à une meilleure compréhension des succès et des difficultés.
- Analyse comparative des données pré/post intervention.
- Recueil des retours des parties prenantes.
- Identification des écarts et des anomalies.
Act : Standardisation ou ajustement des solutions
Selon les résultats, l’organisation s’engage à formaliser les pratiques qui ont démontré leur efficacité ou à revenir en arrière afin d’envisager de nouvelles pistes d’amélioration. DHL illustre bien cette étape en intégrant les bonnes pratiques dans ses procédures standards, tout en nourrissant une culture d’adaptation permanente.
- Formalisation des pratiques réussies.
- Formation continue des équipes.
- Création d’une boucle de feedback permanente.
Étape | Actions clés | Exemple d’entreprise |
---|---|---|
Plan | Analyse SWOT, définition des objectifs, planification | Nestlé |
Do | Test sur petite échelle, documentation | Ford |
Check | Mesure KPI, feedback terrain | Michelin |
Act | Standardisation, formation, ajustements | DHL |
Application pratique de la roue de Deming dans les grandes entreprises : des retours d’expérience concrets
Le succès de la roue de Deming ne s’arrête pas à sa théorie. Il se manifeste pleinement à travers son appropriation par des entreprises d’envergure mondiale. Prenons l’exemple de Sony, qui a utilisé la méthode PDCA pour améliorer la qualité de ses produits électroniques. À travers des cycles répétés, ils ont pu détecter rapidement les défauts, ajuster les processus de fabrication et rehausser la satisfaction client.
De même, Boeing l’a utilisée pour optimiser ses processus de fabrication aéronautique, permettant une réduction significative des coûts et des délais, tout en renforçant la sécurité et la qualité. Ces exemples démontrent comment intégrer la roue de Deming dans une organisation demande de la rigueur mais aussi une implication multi-niveaux, de la direction aux équipes opérationnelles.
- Engagement des dirigeants pour impulser la démarche.
- Participation active des équipes dans l’identification des problématiques.
- Utilisation de données fiables et outils digitaux pour le suivi.
- Adaptation constante du processus selon les retours d’expérience.
Entreprise | Secteur | Application PDCA | Résultat |
---|---|---|---|
Sony | Électronique | Optimisation de la qualité produit | Réduction des défauts, satisfaction client accrue |
Boeing | Aéronautique | Amélioration processus fabrication | Baisse des coûts, sécurité renforcée |
General Electric | Industrie diverse | Gestion qualité totale | Efficacité accrue, amélioration continue validée |
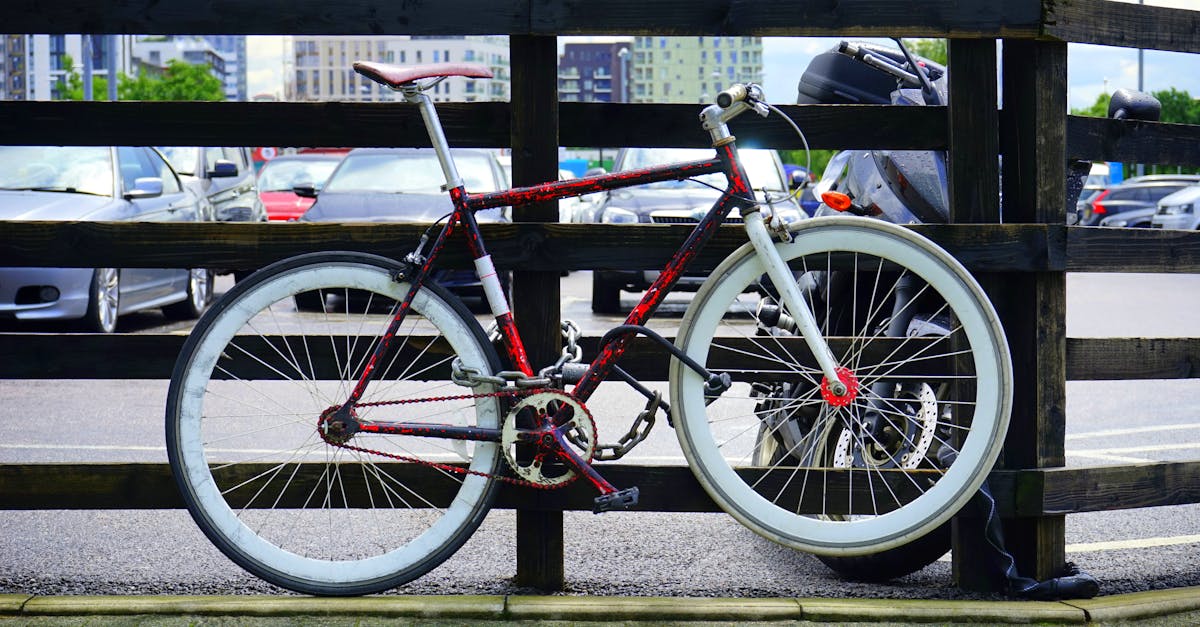
Les avantages clés de la roue de Deming pour piloter l’amélioration continue en entreprise
Intégrer la méthode PDCA au cœur des processus d’une entreprise renforce bien plus que la simple qualité. C’est un moteur multifonctionnel favorisant la pérennité organisationnelle et la compétitivité sur des marchés en constante évolution. Parmi les bénéfices tangibles, plusieurs ressortent clairement :
- Culture de l’amélioration continue : le PDCA instaure un cadre répété qui invite à repenser constamment les méthodes sans se reposer sur des acquis.
- Réduction significative des erreurs : grâce aux cycles d’essai et à la validation systématique, les erreurs sont détectées tôt et corrigées efficacement.
- Mobilisation et engagement des collaborateurs : leur participation dans chaque phase renforce l’appropriation des objectifs et génère un climat de confiance.
- Flexibilité organisationnelle : la méthode favorise une adaptation rapide aux évolutions du marché ou des exigences réglementaires.
Pour illustrer, Mazda a tiré parti du PDCA pour transformer son système de production en une chaîne agile et réactive, lui permettant de répondre plus vite à la demande mondiale tout en réduisant les coûts. En parallèle, Ford a modernisé ses processus grâce à cette méthode, intégrant ainsi amélioration continue et innovation pour rester compétitif face aux nouveaux acteurs technologiques.
Avantage | Description | Exemple |
---|---|---|
Amélioration continue | Réévaluation et ajustement systématiques | Mazda |
Diminution des erreurs | Identification précoce des défauts | Ford |
Engagement des équipes | Participation active à toutes les phases | Nestlé |
Flexibilité | Réactivité aux évolutions et imprévus | DHL |
Défis et limites de la mise en œuvre de la roue de Deming dans les organisations modernes
Bien que redoutablement efficace, le cycle PDCA n’est pas exempt de difficultés dans son adoption et sa pérennisation. Les entreprises doivent anticiper et gérer ces obstacles pour garantir un succès durable. Premier point souvent rencontré : la résistance au changement. Les collaborateurs peuvent être réticents face à une nouvelle méthode, surtout si elle bouleverse leurs habitudes ou les expose à davantage de contrôle.
De plus, la méthode demande un engagement conséquent en termes de ressources, notamment au niveau du pilotage, du recueil de données et de la formation continue des équipes. Pour de nombreuses entreprises, ce coût initial peut freiner les initiatives, surtout dans des contextes de pression budgétaire.
L’évaluation de l’efficacité des changements constitue un autre défi. Isoler l’impact réel des actions du reste des variables organisationnelles est complexe, tout comme la collecte de KPI pertinents et fiables.
- Gestion de la résistance culturelle et managériale.
- Nécessité d’investissement en formation et outils.
- Difficulté à mesurer rigoureusement les effets.
- Complexité de suivi dans des environnements changeants.
Défi | Moyens d’atténuation | Exemple |
---|---|---|
Résistance au changement | Communication transparente, implication des équipes | General Electric |
Coût des ressources | Planification rigoureuse, priorisation des actions | Toyota |
Complexité de la mesure | Développement de KPI adaptatifs, analyse statistique | Honda |
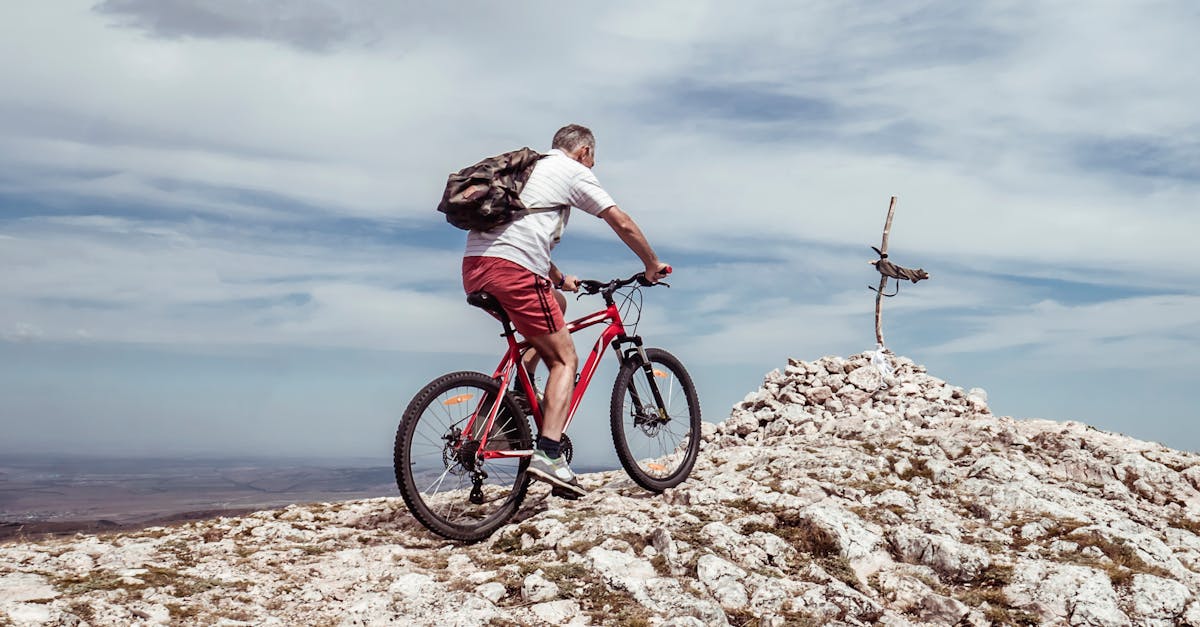
Le lien indissociable entre la roue de Deming et le Lean Management : un duo gagnant pour l’optimisation
La philosophie du Lean Management, popularisée par Toyota, se concentre sur l’élimination des gaspillages et la maximisation de la valeur ajoutée. L’intégration du cycle PDCA dans ce cadre managérial offre une méthode concrète pour tester, valider et pérenniser les améliorations. Ainsi, le PDCA constitue la colonne vertébrale des initiatives Lean chez des acteurs comme Ford, Michelin, ou General Electric.
Les sept types de déchets identifiés en Lean – transports, stocks, mouvements inutiles, attentes, surproduction, surtraitement et défauts – sont autant de cibles pour les cycles continus d’amélioration guidés par la roue de Deming. Cette approche systématique favorise un pilotage dynamique et participatif, impliquant l’ensemble des équipes à tous les niveaux.
- Utilisation du PDCA pour identifier et éliminer les gaspillages.
- Amélioration de la qualité et de la productivité par des cycles itératifs.
- Mobilisation des collaborateurs pour renforcer l’engagement Lean.
- Adaptation rapide par l’analyse continue des processus.
Aspect Lean | Contribution de la roue de Deming | Entreprise illustrant le lien |
---|---|---|
Réduction des déchets | Ciblage précis via le PDCA, actionnement rapide | Toyota |
Qualité renforcée | Tests et ajustements itératifs | Michelin |
Engagement des employés | Participation active dans chaque cycle | Ford |
Intégration d’autres modèles d’amélioration continue issus de la méthodologie Deming
Outre le PDCA, d’autres méthodologies basées sur les principes de Deming ont vu le jour. Le cycle DMAIC, employé dans les démarches Six Sigma, prolonge le PDCA en offrant une démarche plus détaillée et analytique : Définir, Mesurer, Analyser, Améliorer, Contrôler. Cette approche complète est particulièrement utilisée dans les environnements où la maîtrise statistique est essentielle.
Par ailleurs, la norme ISO 9001 incorpore largement la logique de la roue de Deming, en plaçant l’amélioration continue au centre du management de la qualité. Cette convergence démontre la pertinence et la robustesse intemporelle des principes de Deming, adaptés aux exigences modernes de flexibilité et d’efficience.
- DMAIC : extension analytique du PDCA pour les environnements complexes.
- Norme ISO 9001 : intégration des principes d’amélioration continue.
- Approche Kaizen : application régulière du cycle PDCA pour le progrès quotidien.
- Importance accordée à la mesure et au contrôle statistique.
Modèle | Origine | Application principale |
---|---|---|
PDCA | William Edwards Deming | Amélioration continue générale |
DMAIC | Six Sigma | Gestion optimisée de la qualité, analyse approfondie |
ISO 9001 | Organisation internationale de normalisation | Management de la qualité systématique |
FAQ sur la roue de Deming et son utilisation pour l’amélioration continue
- Quelle est la différence principale entre PDCA et DMAIC ?
Le PDCA est un cycle général d’amélioration continue tandis que le DMAIC est une méthode plus détaillée utilisée dans les démarches Six Sigma pour analyser et améliorer en profondeur les processus complexes. - Comment intégrer efficacement la roue de Deming dans une PME ?
Commencez par sensibiliser les équipes, mettre en place de petits projets pilotes, former les collaborateurs et instaurer un système de suivi des résultats avant de déployer à plus grande échelle. - Quels sont les KPIs essentiels à suivre lors du cycle PDCA ?
Ils varient selon les objectifs, mais incluent généralement la qualité (taux de défauts), les délais, la productivité et la satisfaction client. - La roue de Deming convient-elle à des secteurs non-industriels ?
Absolument, elle est applicable dans les services, la santé, la logistique et même les secteurs publics pour améliorer la qualité et les processus. - Quelle est la durée typique d’un cycle PDCA ?
Elle dépend de la complexité des actions mais un cycle peut s’étendre de quelques semaines à plusieurs mois, avec une focalisation sur la rapidité des retours pour accélérer l’amélioration.